What We’re Doing About Our Plastic Problem
Our home planet has a deeply disturbing and pervasive problem with plastics. In April, a group of researchers studying the deepest part of the ocean—the Mariana Trench—discovered plastic bags and candy wrappers floating nearly seven miles below the surface of the Pacific Ocean.
Globally, about 450 million metric tons of plastic are produced every year and 9.5 million tons of plastic are thrown into the ocean annually, most of it single-use. Both these numbers are on the rise. A report from the Ellen MacArthur Foundation says by 2050 there will be more plastic in the oceans than there are fish (by weight).
Patagonia has always had a plastics problem, too. We’ve made significant progress on recycling the high-quality polyester and nylon we use in many of our best products—in 1993, Patagonia was the first outdoor clothing manufacturer to transform trash into fleece. We are constantly evaluating new materials and reevaluating existing ones. When the best available materials aren’t good enough to meet the need, we work closely with our suppliers to develop outstanding new fabrics.
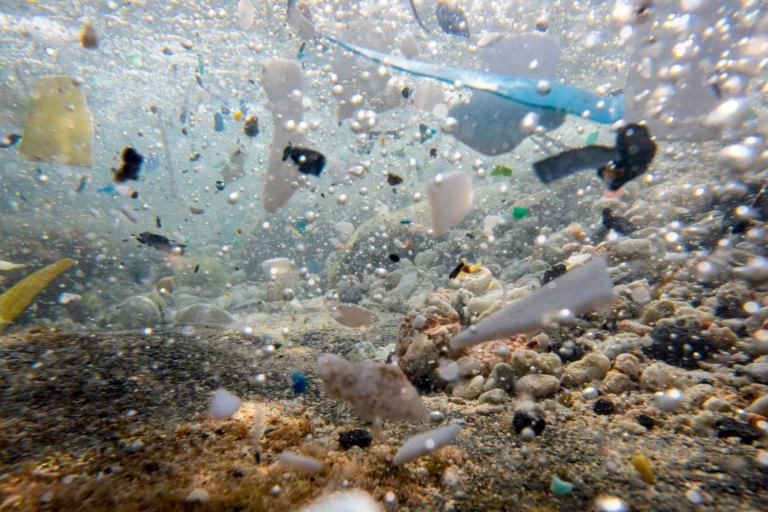
We’re investigating biodegradable synthetic fibers as a solution to microfiber shedding from washing garments. Our tests have shown us how complex biodegradation is depending on the environment where a garment meets the end of its life, but also on what type of finishing is applied to the fabric and also on what type of test method we’re using. Photo Jim Hurst
Polyester has undeniable benefits, says Ryan Thompson, Patagonia’s manager of materials R&D for the technical knit, naturals and trim categories. “In historic alpine insulation systems, the material of choice was almost always wool,” says Thompson. “The transition to polyester happened because we could offer an economical alternative to wool with similar performance and comfort characteristics.” While wool takes days to dry out, polyester can keep you safe and dry if the weather shifts in the backcountry. Thompson notes, “It’s a great material to layer. We can manage polyester’s affinity to water, it’s durable even at light weights and it’s easier to maintain because it’s machine washable and dryable.”
Today, our materials team uses recycled polyester made from used soda bottles and unusable manufacturing waste to create new polyester fibers for clothing. And our extensive field testing shows it performs just as well, if not better, as gear made from virgin polyester. Using recycled fabrics limits our dependence on petroleum as a source of raw materials and prolongs landfill life, while also reducing toxic emissions from incinerations. This fall, 69 percent of all Patagonia materials will be derived from recycled materials. Switching to recycled from virgin materials also means we’ve reduced our carbon footprint by 13,000 tons of CO2e. Our goal is to use only renewable or recycled materials in our products by 2025.
To solve our plastic pollution problem at its root, we are partnering with scientists, researchers and other apparel companies. Our gear and care guides are meant to inform customers on how to keep gear in play longer. Our supply chain stories tell the reality of what goes into making clothes—our effort to educate customers to make informed shopping decisions. By talking openly about our trials and failures in minimizing our impact, we hope to inspire solutions and collaboration within the clothing industry.
Microfibers
Microfibers are tiny fibers five millimeters or smaller that fall from synthetic garments—such as polyester fleece or nylon shorts—during washing and can get past or around the filtration system in treatment plants and end up in the ocean, on beaches and in rivers and lakes, and sometimes settle in places where they don’t belong, like in the belly of a fish.
Patagonia first found out about microfibers in 2011 when research from marine biologist Dr. Mark Anthony Browne at UCSB found high concentrations of microplastics, specifically fibers, on beaches all around the world. Fleece was initially flagged as the main culprit, but we have since learned that all fabrics contribute to the problem. Both synthetic and natural materials produce shedding during washing, and scientists are still looking into the impact of microfibers coming from different materials. Whereas natural fibers eventually biodegrade, synthetic ones do not, which adds to the growing plastic problem in our oceans.
To date, we have funded five projects looking at solutions to pollution from microfibers. We charged our own materials development team to identify fiber types and construction techniques that minimize shedding. To aid that effort, we commissioned a study from North Carolina State University to help us understand which characteristics in fabrics lead to microfiber release—and to develop a rapid test methodology to assess the potential of fabrics to shed during laundering. Most recently, we partnered with REI, MEC and Arc’teryx to commission a study from the nonprofit Ocean Wise, the Vancouver Aquarium and Metro Vancouver on the effectiveness of that region’s wastewater treatment plants at filtering microfibers. We’ve been writing all about these efforts and what we learned on our blog.
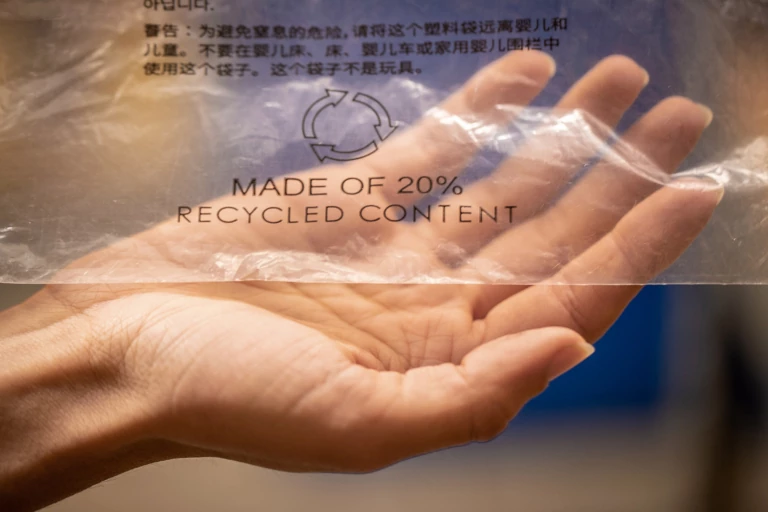
Your curbside recycling program will most likely not recycle this polybag we use to package Patagonia products, but most chain supermarkets can and so do all our stores. Polybags are made from plastic film and ours use 20% recycled content. Next spring, all our polybags will be made from 100% recycled content. Photo: Tim Davis
Plastic packaging
Patagonia uses polybags to individually wrap products from our factories, to provide protection during shipping and handling. Polybags are made from polyethylene film (plastic film #4 or LPDE film), a type of plastic not commonly recycled in curbside recycling systems throughout the United States.
City recycling systems may not be able to recycle this plastic, but we’ve found suppliers who can. In spring of 2020, the polybags we use to package our products will be made of 100 percent recycled content which will be Global Recycle Standard (GRS) certified.
We encourage you to also recycle the polybags that come with your products. Most chain grocery stores have bins at the entrance of their stores to collect used plastic grocery bags. The polybags used to package Patagonia’s garments can be recycled with grocery bags. You can find recyclers in your area on Earth 911.com.
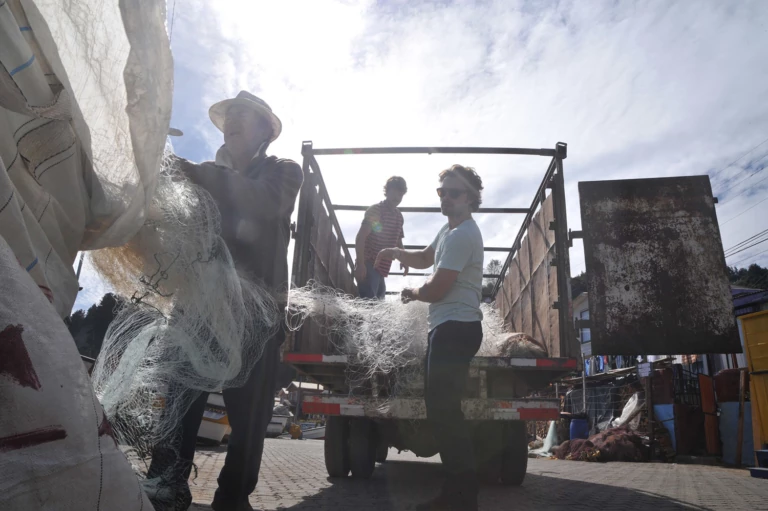
The Great Pacific Garbage Patch lies somewhere between Hawaii and California and is predicted to contain at least 87 thousand tons of plastic. 46 percent of this plastic is made up of discarded fishing nets. Bureo, a company based in Ventura, California, collects discarded fishing nets through a traceable supply chain in South America and recycles them into material for skateboards, sunglasses, and surf fins. Photo: Courtesy Bureo
Keeping plastic out of the ocean
Through our Tin Shed Ventures® fund, we invested in Bureo®, a company based in Ventura, California, which collects discarded fishing nets through a traceable supply chain in South America. Bureo recycles these nets into NetPlus™ material and turns them into skateboards, sunglasses and surf fins. We are now collaborating with Bureo to integrate their material into Patagonia hard-goods and textiles. So far, Bureo has diverted more than 6.8 million square feet (over 500,000of fishing nets from the coastlines of South America.
Biodegradable plastic
“Biodegradable” and “compostable” claims appear on many consumer products—from detergents and flowerpots to plastic bags and even textiles. But because of the different ways we dispose of solid waste (in the US we typically send waste to landfills, while in Europe it is common for waste to be incinerated), these products are rarely given the chance to decompose.
Biodegradable means a material will break down through microbial action into basic elements found in nature. That is, they must be “eaten” by microbes, such as those found in soil, and the decomposition must occur relatively quickly. Many materials will degrade over time from sunlight, heat, moisture and mechanical stress, but this alone is not biodegradation.
Natural products are perceived to be inherently biodegradable, but this is not necessarily true. For example, leather is made by “tanning” animal skin into a durable product but takes between 25 and 40 years to break down. Cotton fiber is biodegradable, but a cotton shirt has other components that may not be. Sewing thread is often polyester or cotton wrapped around a polyester core, and buttons are most commonly made of plastic or metal. Even the dye that gives color to the cotton may be an issue when the fibers degrade and leave microscopic amounts of dye in the soil. Plastic and synthetic materials can be made with additives to help them degrade faster. But if they don’t fully break down into basic elements, the resulting “microplastic” can pollute the environment.
Since 2015, we’ve been investigating biodegradable synthetic fibers as a solution to microfiber shedding from washing garments. Patagonia commissioned a third-party study with Belgium-based OWS to evaluate the biodegradation behavior of our existing and future fiber materials in the marine environment. Through this research we’ve identified just how complex biodegradation in varied environments is depending on test method, textile finishing or environment (marine, landfill, wastewater treatment, industrial compost).
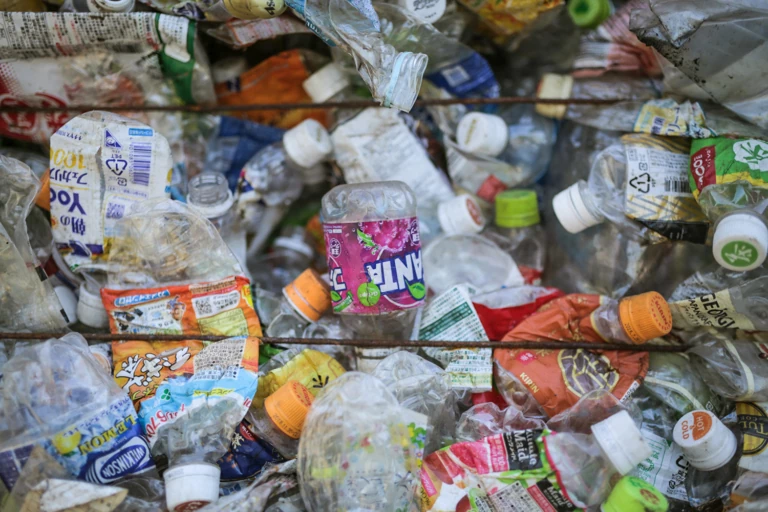
Using recycled polyester not only keeps plastic out of landfills, but also reduces our carbon emissions by 40 percent compared to using virgin materials that are directly extracted from petroleum. And our extensive field testing shows recycled performs just as well, if not better, as gear made from virgin polyester. Photo: Lloyd Belcher
The results did not conclusively show that the biodegradable synthetic technologies we tested biodegrade in the marine environment. The marine environment is so varied that an appropriate test method to correlate to the real world is challenging—we know we need to crack that nut if we want to make any definitive claims. Additionally, our testing showed that wool, widely regarded as a natural and biodegradable fiber, did not break down in the marine environment. Based on these tests, we are unconvinced that minor modifications to synthetic fibers could dramatically increase the biodegradation rate in the marine environment.
At this point, biodegradation has not proven to be a solution to microfiber pollution. We want our products to have a long life and to be durable and reliable. We will continue to look for new technology for biodegradable materials and to work with academia and other makers to evaluate them. It’s a serious challenge, but an exciting one.
The day will come when polyester and nylon clothes from Patagonia will be sourced entirely from some of the 6 billion tons of plastic already circulating the planet. Or these fabrics will come from natural sources, plants grown in a way that does not reduce the production of food. Completely recycled or bio-based polyester and nylon will likely still come at some environmental cost, but one far less dear than the one we all face for the convenience and advantages of plastic.