Giving Workers More of a Voice
Behind everything we make is the hard work of a human being—from growing raw materials and weaving fabric to cutting and sewing the finished product. Yet those who work in garment factories—and, globally, more than 60 million people do—have historically been subject to substandard working conditions and unable to report those issues. That’s why, in 1996, Patagonia joined as a founding member of the Fair Labor Association (FLA)—an organization dedicated to improving labor practices in the apparel industry—and why we’ve made it our mission to ensure fair and safe working conditions for every person behind our products. Even so, we can’t do this from the top down. If we’re really going to do right by the workers in our supply chain, we have to give the workers themselves more of a say.
Factory by factory, we’ve worked to put programs in place to enable workers to stand up—and speak up—for their rights. While trade unions are an important tool to ensure workers have a voice through collective bargaining, not all factories can be unionized, so we’ve had to find new ways to promote the voices of our workforce.
Fair Trade Starts Conversations with Managers
Introducing our first Fair Trade Certified™ sewn products in 2014 was an important step. Through Fair Trade, participating brands pay a premium for every product made in factories certified to the Fair Trade standard. Those funds are managed by a democratically elected worker committee that comes together to voice opinions on how to spend the money after assessing the needs of the workers in the factory, and ultimately decides how it’s spent. For the first time in many workers’ lives, this process opens up conversations with management about critical issues affecting their day-to-day lives.
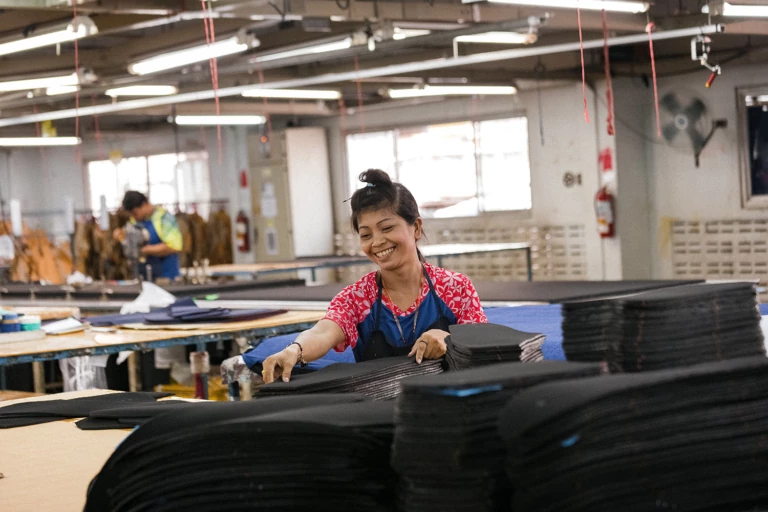
Photo: Ryan Craig
In a Fair Trade Certified™ factory in India at a worker committee meeting in 2014, workers shared some basic needs that often get overlooked. Many wanted to find a way to stay dry when commuting to the factory during the upcoming monsoon season. Workers who lived in factory-provided housing wanted a shared kitchen to be able to cook their meals. These same workers also wanted lodging for their families who visit them over the weekend. After hearing their needs, factory management committed to paying for a shared kitchen facility and reserved several rooms especially for visitors, which enabled workers to use their Fair Trade premiums to purchase raincoats. Through this process, much-appreciated improvements were made.
Installing Safe, Trusted Ways to Make Change
In order to make this happen in all of our factories, we set out to develop our Grievance System Toolkit—a series of training, guidance and assessment documents that our factories use to ensure workers can freely share their concerns with management, and that these issues will be addressed in a timely manner. Using the toolkit, each of our factories has considered the best grievance mechanisms to put in place for their unique circumstances, including worker committees, trained complaint handlers, regular worker forums or surveys, open-door policies and hotlines.
“The more high-quality, trustworthy mechanisms a factory can offer, the better,” says Wendy Savage, Patagonia’s director of social responsibility and traceability. “Giving workers more ways to share their concerns increases their chances of doing so. An open-door policy is not enough. A survey is not enough. We want them to have many choices to voice their concerns, so they feel comfortable and begin to establish trust with factory management.”
The system outlines four maturity levels for factories to reach. A factory designated as “Red” does not have an adequate grievance system in place and must work to put systems in place. Any factory that meets Patagonia’s minimum “Bronze”-level requirements has at least two appropriate grievance mechanisms workers can access, one of which is anonymous. A “Silver” designation has multiple grievance mechanisms offered, regular trainings in place, and makes continuous improvements based on grievances and other types of feedback that the factory proactively solicits from workers. A “Gold”-level factory has met all the requirements above, but also makes grievances available to the public, and requires that third parties and workers are involved in reviewing their system to make improvements. The system sets clear levels of expectation for these factories to aspire to—and gives them the guidance to do so.
“I wouldn’t say what we’re doing is revolutionary. It’s a simple and pragmatic way to improve grievance systems at the factory level and build trust over time between workers and management,” says Alexander Katz, manager of supply chain social responsibility. “Our program requires deep knowledge of a factory’s systems and dedicated manpower to follow up on issues. By establishing long-term and continuing relationships with our suppliers, we’re able to work closely to build effective mechanisms that are tailored to each factory.”
“It’s a safe space, where workers can speak their minds. They can talk freely about what they think their fellow workers need, and then they vote on it. Through this process, factory management gets to hear what their needs really are,” says Thuy Nguyen, manager of social responsibility and special programs at Patagonia.
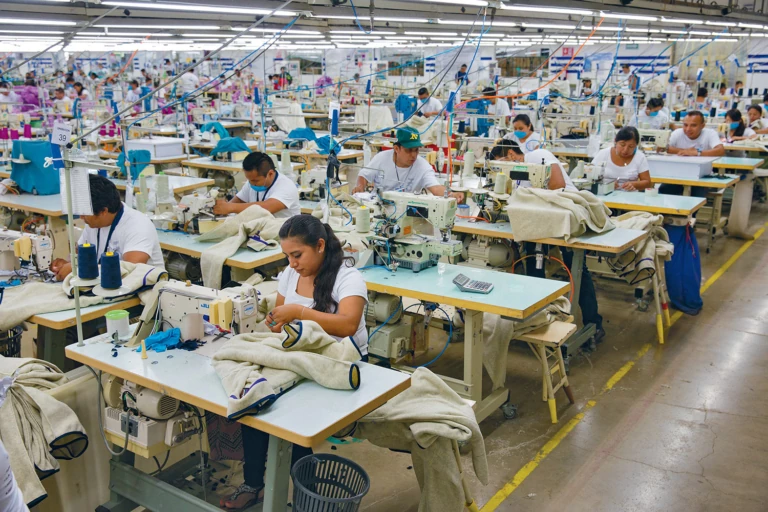
Workers at the Fair Trade Certified™ Hong Ho factory where Patagonia fleece is made in Valladolid, Mexico. Photo: Keri Oberly
Tailoring Our Approach
As part of this commitment, we felt that it was important to put people on the ground to build relationships and establish this level of trust. In 2012, Patagonia hired three field managers to support every finished goods factory making Patagonia products.
Over the past six years, Jeraporn Rothong has worked as a Patagonia field manager covering 20 factories in four countries (Sri Lanka, Bangladesh, Thailand and India). So far, she’s helped move almost all of these factories from Bronze to Silver, and two of them to Gold. “We understand this is not easy for the factories, and it’s hard to implement such a high standard,” says Rothong, “but ideally all factories should be Gold.”
Each field manager conducts regular audits, including factory walk-throughs and interviews with workers and management to collect different perspectives. They check in regularly, assess grievance system maturity levels, work together to find solutions, and monitor progress with each factory, one by one.
“When we first introduced the guidelines, it was a bit intimidating,” says Rothong. “The more we talked to them, the more they understood our intention, which was ultimately to improve working conditions in the factory. It wasn’t that we wanted to blame them.”
In addition to the grievance mechanisms implemented and monitored at the factory level, Patagonia set up a supply chain hotline. Accessible for any worker in the world to call in at any time, the line allows field managers to investigate every incident, find out why it happened, visit the factory, figure out a solution and protect the worker. As part of its accreditation, FLA reviews the grievances Patagonia receives every year to be sure they follow up on every call.
When a call came in from a factory this year, we learned that workers were nervous about the future of that factory, reporting rumors that it may be closing. We were able to talk to factory management directly and reassure the workers that the factory was not closing. “I’m happy the workers trust us, but I would be happier if they felt comfortable asking management. This kind of example shows us that the factory has some gaps, that workers and managers don’t feel like they can talk to each other about everything,” Rothong says. “We encourage the factories and workers to address issues internally when they can, but if they can’t, we have systems like this in place so that workers can still raise issues with us.”
Rothong believes that all the factories we work with welcome our support in reaching higher levels of maturity to handle grievances. “I think they know that we really care about the workers,” says Rothong.
Sharing Our Learnings
To encourage other brands to implement programs that elevate workers’ voices and actively work together to change conditions for workers in the apparel industry, Patagonia has shared its Grievance System Toolkit with them. We’ve also shared best practices and learnings from implementing Fair Trade certification in what now represents more than 40 percent of our total product line, with more Fair Trade Certified™ sewn products than any other outdoor apparel brand.
In our latest effort to hear from our factory workers, we will be piloting digital surveys to gather their feedback on our fire safety and prevention program, one of several worker welfare programs we have in place. While this approach can help us gather worker feedback relatively quickly, we also realize its inherent limitations. It doesn’t build the personal connection that’s needed with workers to talk about deeper issues that require trust and confidence to resolve. Because every factory is different, it will be essential for us to continue to have a suite of tools we can use to engage with workers to gather meaningful feedback that will be supported by factory management.
“To have the greatest impact we will need help from other brands to scale worker engagement programs until they become the norm in the industry,” says Nguyen. Nguyen believes the people with the most power to drive this change are perhaps the voice that brands value the most—the customer’s. “We can buy Fair Trade products and use our purchasing power to show our favorite brands that these things are important to us. We can reach out and ask them to be transparent about what goes on in their supply chain.”
While we’ve made great progress, in many ways our work has just begun. While the grievance system program is in place for all our finished goods factories, we’re working on moving raw material factories into the process, too. Our goal is for all suppliers to have these systems in place, no matter what it takes.
“Every day, we’re in meetings where we talk about the right thing to do, and sometimes, it means we need to start from scratch—but we do it, every time,” says Nguyen. “It’s a lot of work and we have a long way to go, but we are beginning to see results.”
Visit patagonia.com/fairtradeclothing to see the entire collection.